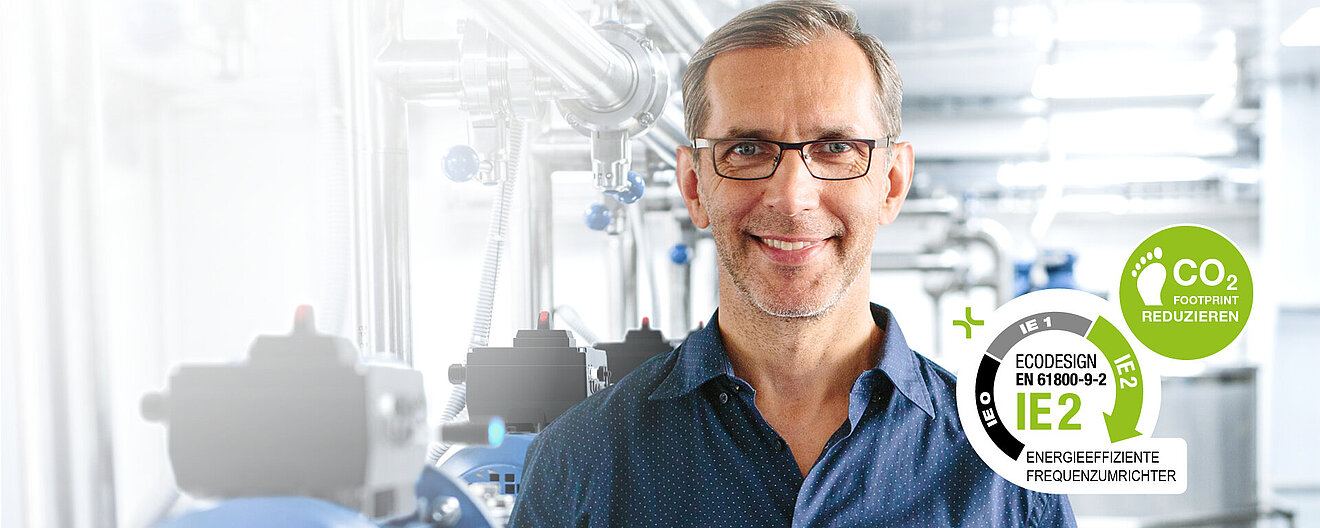
Reduce energy costs up to 50%
Save money and energy through motor control and simple retrofitting in existing systems.
Control motors in industrial plants
Do you actually know that motors that run unregulated on the mains waste valuable energy?
An uncontrolled motor runs at 100 % power even if only 50 % are needed. To counteract this energy waste, you do not have to replace your entire machine park. You can simply retrofit your motors that are currently operated on the mains with a frequency inverter. Our motor-mounted INVEOR frequency inverters control the motor power and thus reduce energy consumption. They reduce running costs and improve the CO₂ footprint of your production. This means that you meet all the requirements of the Ecodesign Directive and can also relax in the face of future tightening.
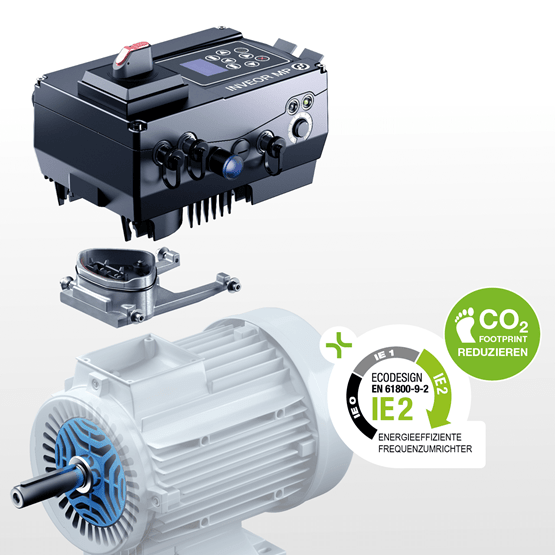
The INVEOR offers you the following benefits:
Fits into any system
You do not need any additional infrastructure such as a control cabinet and do not have to lay long cables to the drives. The INVEOR is mounted directly on the motors.
Controls all motor types
Quickly mounted on the motor with the matching adapter plate, the INVEOR controls all motor types, regardless of manufacturer, efficiency class or motor technology.
Fit for the future
Save energy immediately with your existing drives. When modernising your machinery in the future, simply continue to use the INVEOR for the new motors.
Easy installation
With the Selfcom function in INVEOR, the inverter recognises the motor automatically without having to carry out time-consuming parameterisation.
Competent expert advice
We will not leave you on your own when it comes to retrofitting and will be happy to support you from the planning to commissioning and are also at your side during operation. Benefit from over 25 years of experience in the development of frequency inverters for industry.
Your investment pays off – both economically and ecologically
Learn here what you can save.
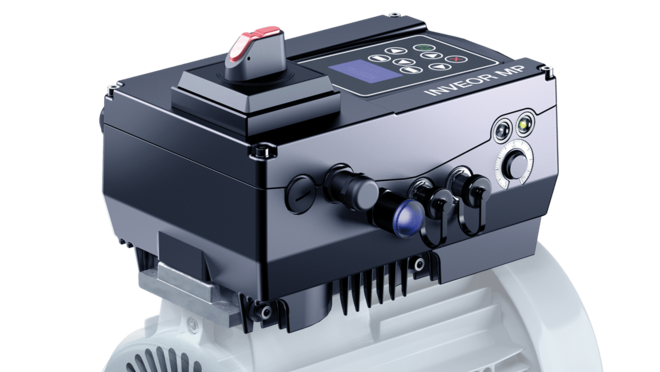
ROI <9 months
Savings per year through frequency inverter 4.300 kWh
Exemplary load scenario
In the following example, in addition to running at full load, an 11 kW motor also runs at partial load for 20 hours per week, requiring 100% of torque but only 50% of speed. During these 20 hours of partial load operation, savings can be generated through the use of an INVEOR frequency inverter, which would be wasted in pure mains operation with 100% power.
In this concrete example, 1.300 € in loss costs (electricity price 0.23 € per kWh) and 2.1 tonnes of CO₂ can be saved in one year. If the motor runs more than the assumed 20 hours per week at partial load or if the motors are larger, the savings potential increases even more.