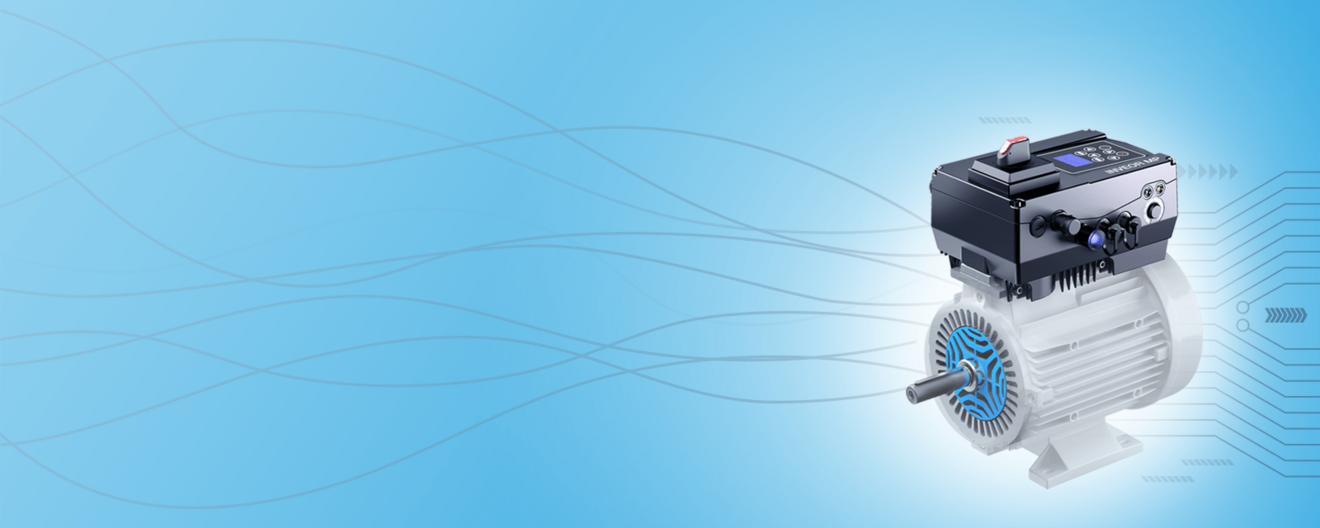
The pulse injection method from KOSTAL: Revolutionary control technology for variable frequency drives
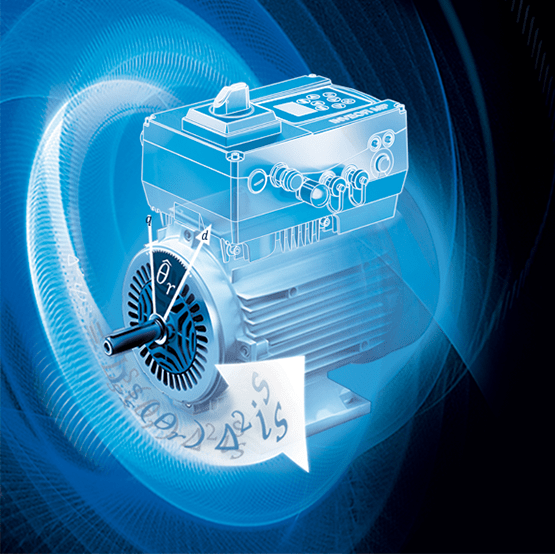
Maximum control performance without limits
Through the innovative pulse injection method, KOSTAL is reinforcing its claim to be a leader in sensorless control technology. Our variable frequency drives therefore achieve a performance that is otherwise only reserved for encoder-based systems – and does so without a single sensor. The control process supports all motor types, from asynchronous and permanently excited synchronous motors to reluctance machines.
In addition to standard winding topologies with distributed windings, motors with cost-effective concentrated windings can also be operated with the INVEOR drive controller, not only with the highest performance levels but also with maximum efficiency. Very high efficiencies of up to IE5 are achieved. KOSTAL variable frequency drives are already preparing you for future, more stringent Ecodesign Directive requirements.
Elimination of the overload limit
A unique feature on the market is the fact that there is no overload limit. Whereas in the past motors had to be oversized in order to handle short-term overloads, the pulse injection method is no longer constrained by any overload limits. This means that the motor can also be smaller. Thanks to the second-generation pulse injection method, the rotor position can be precisely determined on the basis of the motor's anisotropy behaviour even at standstill – and performance levels remain high. In addition, the positional accuracy improves as the current increases, which is revolutionary compared with the methods currently on the market.
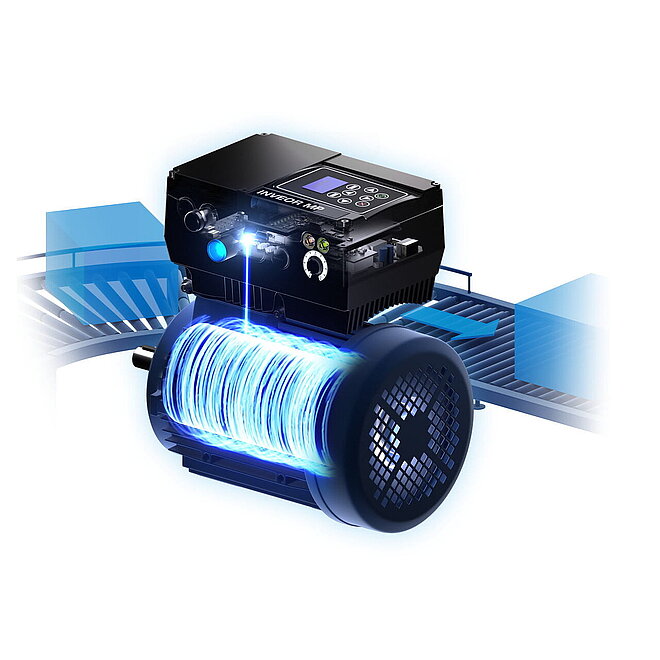
Sensorless positioning without rotor position encoder with KOSTAL ISP
This means that positioning applications are now also possible, and there is no need whatsoever for a rotor position encoder. The door is then opened to further possible applications, from slow positioning to the same position to fast positioning with high dynamics.
Further advantages of the KOSTAL pulse injection method
The new control method also comes with other advantages: by removing the encoder, the motor size is reduced and both shaft ends can be used. The reduced number of components and cable connections also increases the product's life expectancy and system's robustness. This is particularly interesting for applications that are not so well suited to using an encoder.
As the sensor is a very sensitive component in the drive train, problems or even failure may occur in environments with unfavourable ambient conditions, such as vibration, humidity, heat, cold or dust.
Since both the costs of the encoder hardware and the work involved in mounting, adjusting and maintaining the encoder are eliminated, a significant cost saving can be achieved by using the new control process. This even allows the variable frequency drive to be used in harsh environmental situations that were previously not possible with encoder systems.
You also no longer have to worry about matching the variable frequency drive and motor perfectly. The adjustment takes place automatically with the aid of automatic configuration and motor recognition (Selfcom). This vastly simplifies commissioning and parameterisation.
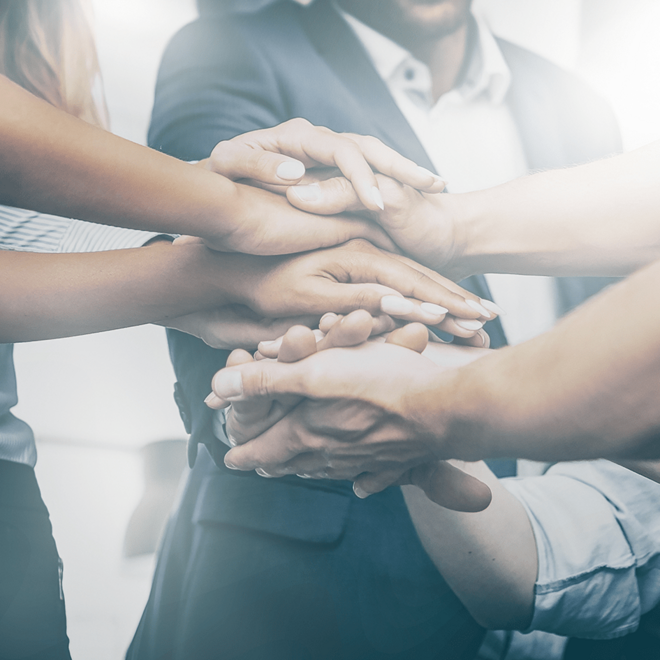
Key features of the KOSTAL pulse injection method:
Do you have any questions about our variable frequency drives?
Complete our contact form or give us a call. We will answer your questions and help you to implement the right frequency inverter solution in your company.
KOSTAL support for new and potential customers
KOSTAL Industrie Elektrik GmbH & Co. KG / Business Unit Drives
Lange Eck 11
58099 Hagen, Germany
+49 2331 8040 - 468 sales-industrial@kostal.com
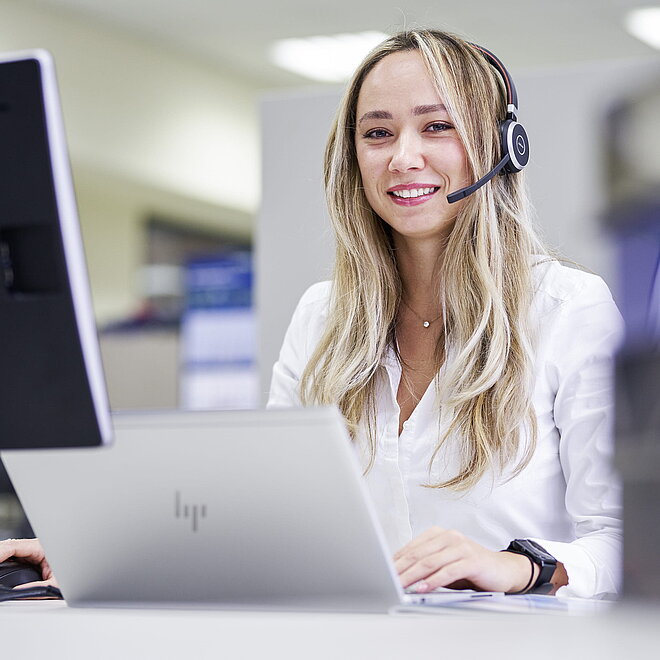