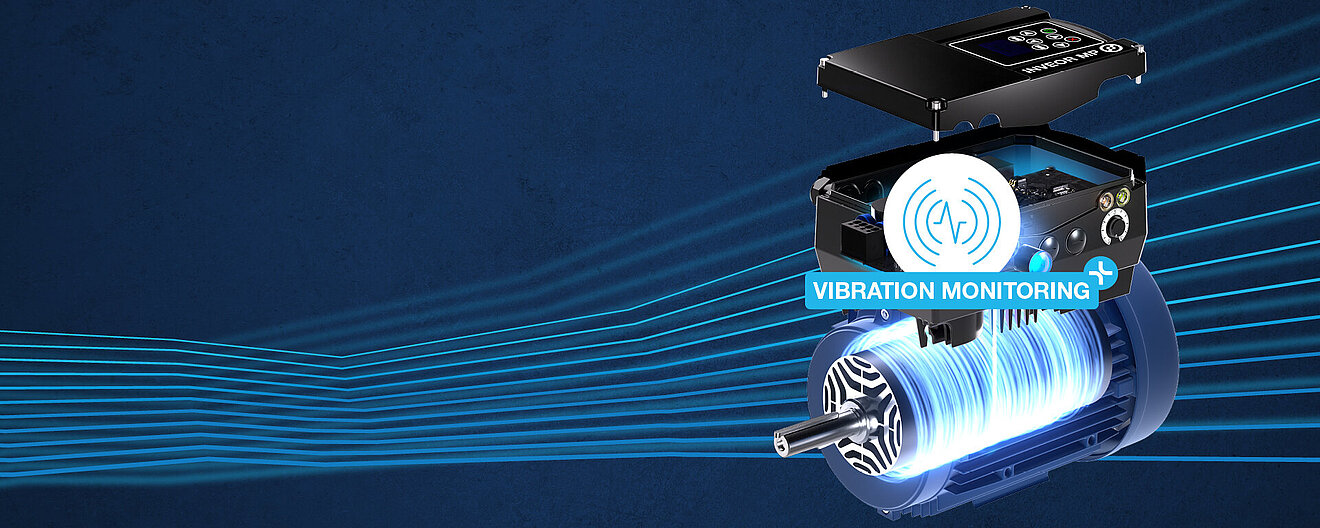
Vibration Monitoring
Save costs through predictive maintenance
Vibration Monitoring
Collecting and analysing data is becoming increasingly important in today's world. With the "Vibration Monitoring" function integrated into the frequency inverter, the INVEOR helps to keep a constant eye on the condition of the system and take the step towards predictive maintenance.
Why vibration monitoring?
- Production plants consist of many individual components.
- Each of these components is susceptible to wear and mechanical problems that can lead to defects and, in the worst case, to a complete shutdown of the system.
- To prevent such defects, systems are normally serviced at fixed intervals.
- It would be more economical to maintain the system as required rather than at fixed intervals.
- The vibrations measured in the system are a key indicator of the need for maintenance.
- Continuous monitoring of the system through "Vibration Monitoring" enables precise identification of maintenance requirements, thus minimising costs and productivity restrictions.
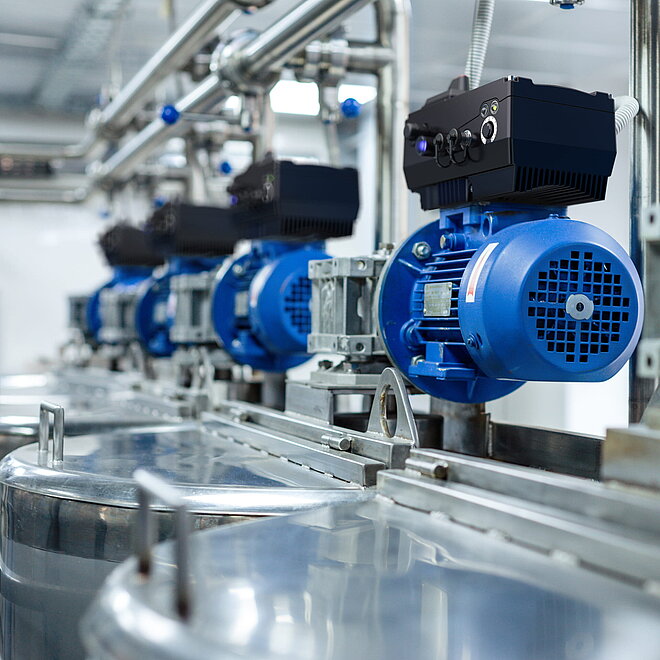
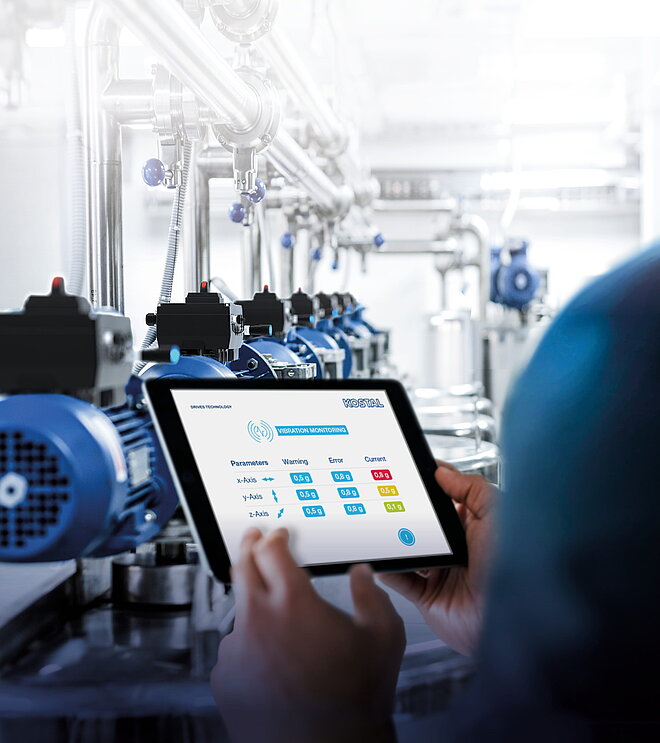
Vibration monitoring - The smart fitness tracker for your system
- Vibration Monitoring" monitors your application during operation for irregularities caused by vibration.
- Like a fitness tracker that monitors your heart rate, INVEOR keeps a constant eye on the "state of health" of your system.
- Potential problems such as progressive wear or the imminent failure of mechanical components can be recognised at an early stage.
- The "Vibration Monitoring" feature is integrated directly into the frequency inverter. Compared to the competition, there is no need to purchase and install a sensor separately. This saves time and money.
- Vibration monitoring is already available as an option in the MPP and is still being planned for the INVEOR MPM.
Getting started with predictive maintenance
- “Vibration Monitoring" records vibrations in the application.
- A PT1000 resistance temperature sensor can be used to monitor temperatures from -20°C to +250°C in the application.
- In addition to this data, the following actual values and process variables available in the inverter can be monitored: Target frequency, actual frequency, mechanical speed, motor current, motor voltage, all digital and analogue I/Os, torque, motor power, operating time, customer-specific PLC output variables.
- The data provided can be transferred to a terminal device or the cloud via fieldbus (EthernetIP, ProfiNet) or MQTT
- Data analysis with INVERTERapp or INVERTERpc software
- Early detection of anomalies and countermeasures - your entry into predictive maintenance.
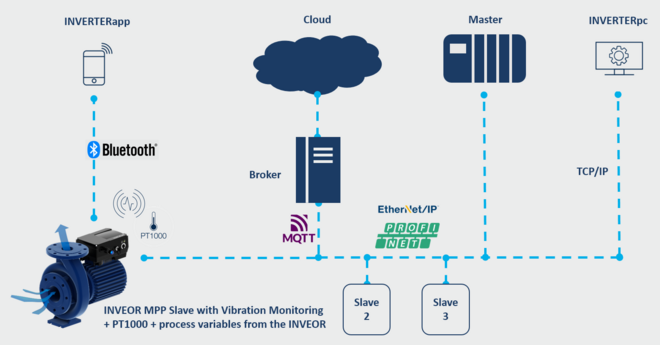
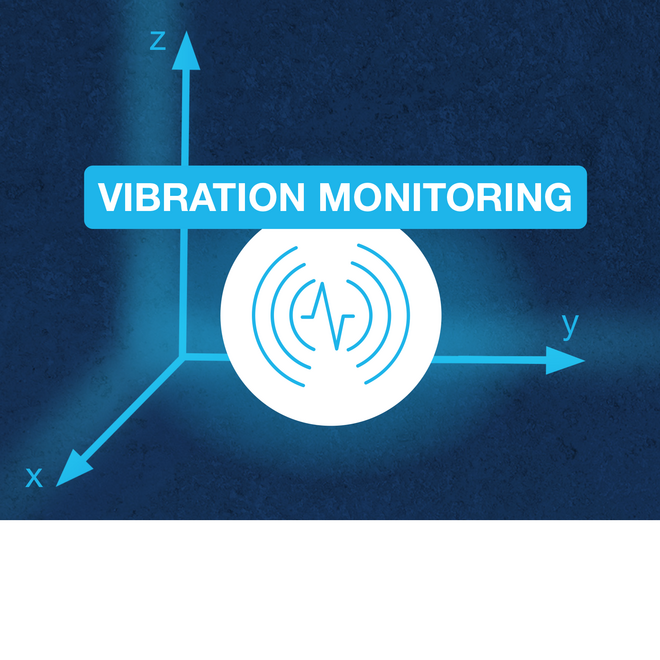
Advantages for the customer
- Function completely integrated into the frequency inverter
- Reduction of downtimes
- Reduction in maintenance costs
- Optimum utilisation of the system's service life
- Increase the reliability and efficiency of the system
- All process variables from a single source
- Future-proof and fit for predictive maintenance
Do you have any questions about our variable frequency drives?
Complete our contact form or give us a call. We will answer your questions and help you to implement the right frequency inverter solution in your company.
KOSTAL support for new and potential customers
KOSTAL Industrie Elektrik GmbH & Co. KG / Business Unit Drives
Lange Eck 11
58099 Hagen, Germany
+49 2331 8040 - 468 sales-industrial@kostal.com
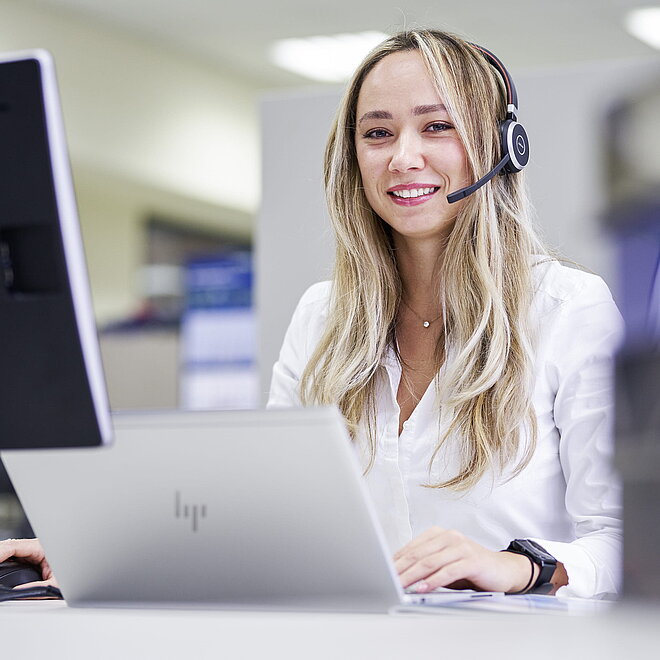